The Benefit of Automated Storage/Retrieval Systems (AS/RS) in Manufacturing
Author Sticky
With 30+ years working with the largest OEM automakers and suppliers, GE Vernova has developed many manufacturing solutions, deployed at thousands of sites around the world.
Often these solutions have value that extends far beyond automotive manufacturing. An example of an application that we’ve deployed with customers is bank management automation – consisting of various configurations such as multiple lane banks and an Automated Storage/Retrieval System (AS/RS). This type of solution benefits automotive manufacturers but also any manufacturer with improved storage capacity and throughput needs.
What is an AS/RS?
An AS/RS system is typically an arrangement of two banks of storage cells with a crane/lift separating the banks. The system allows for incoming items to be put into any available storage cell, and based on demand, any item can be retrieved directly.
AS/RS can consist of multiple banks and cranes based on storage and throughput requirements. The storage banks make use of vertical space within a manufacturing facility in order to decrease horizontal space requirements.
Often these solutions have value that extends far beyond automotive manufacturing. An example of an application that we’ve deployed with customers is bank management automation – consisting of various configurations such as multiple lane banks and an Automated Storage/Retrieval System (AS/RS). This type of solution benefits automotive manufacturers but also any manufacturer with improved storage capacity and throughput needs.
What is an AS/RS?
An AS/RS system is typically an arrangement of two banks of storage cells with a crane/lift separating the banks. The system allows for incoming items to be put into any available storage cell, and based on demand, any item can be retrieved directly.
AS/RS can consist of multiple banks and cranes based on storage and throughput requirements. The storage banks make use of vertical space within a manufacturing facility in order to decrease horizontal space requirements.
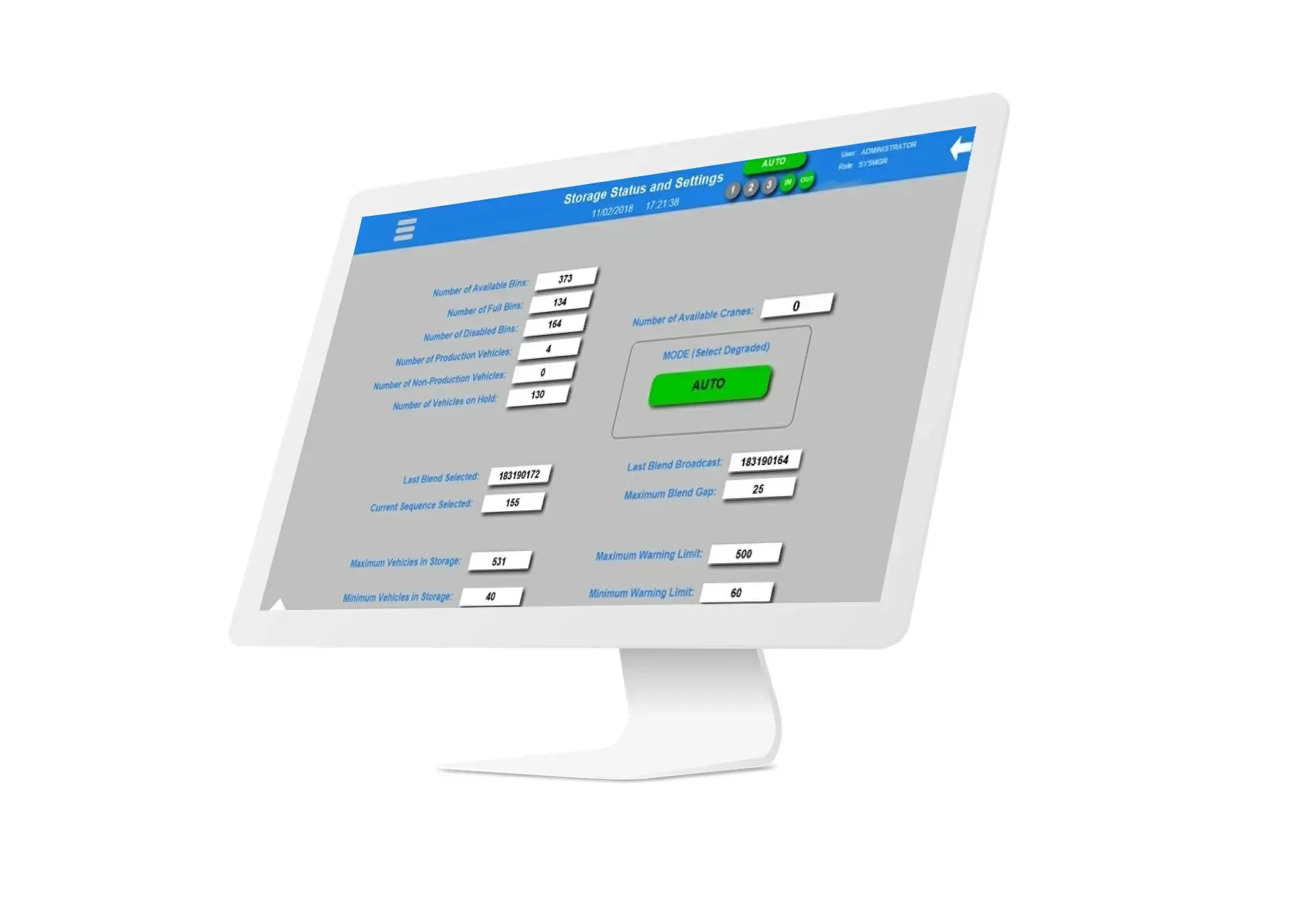
The main screen of this example AS/RS system provides overview statistics of the AS/RS process
Think of a storage bank as a mini warehouse, buffering areas of production so that disruptions in one part of production do not immediately affect other areas. Additionally, the buffers can be used for resequencing material flow to optimize various production areas.
There is a storage area and a system in order to store and retrieve the items – designed for speed and efficiency. In the automotive examples where vehicle bodies are stored/retrieved, crane systems are used. However, AS/RS systems can provide value in many different types of manufacturing.
There is a storage area and a system in order to store and retrieve the items – designed for speed and efficiency. In the automotive examples where vehicle bodies are stored/retrieved, crane systems are used. However, AS/RS systems can provide value in many different types of manufacturing.
Benefits
Advantages of automated storage and retrieval systems
Some of the benefits of implementing an AS/RS system include:
Some of the benefits of implementing an AS/RS system include:
- Compact footprint – Having an AS/RS can improve the capacity of the facility as material can be stored more efficiently. In a large facility, materials can be stored on top of each other up to the rafters in a manufacturing facility.
- Reduce user error in selecting material – Utilizing technology and using rules, material selection can be done correctly and efficiently every time, also reducing search time for material.
- Increased throughput – Material can be selected faster and more efficiently which allows faster material delivery.
- Greater inventory control – More efficient storage allows manufacturers to know easily where material inventory is.
- Manufacturing buffer – An AS/RS allows production to keep running if the feeding system goes down. This provides a safety net for production to continue.
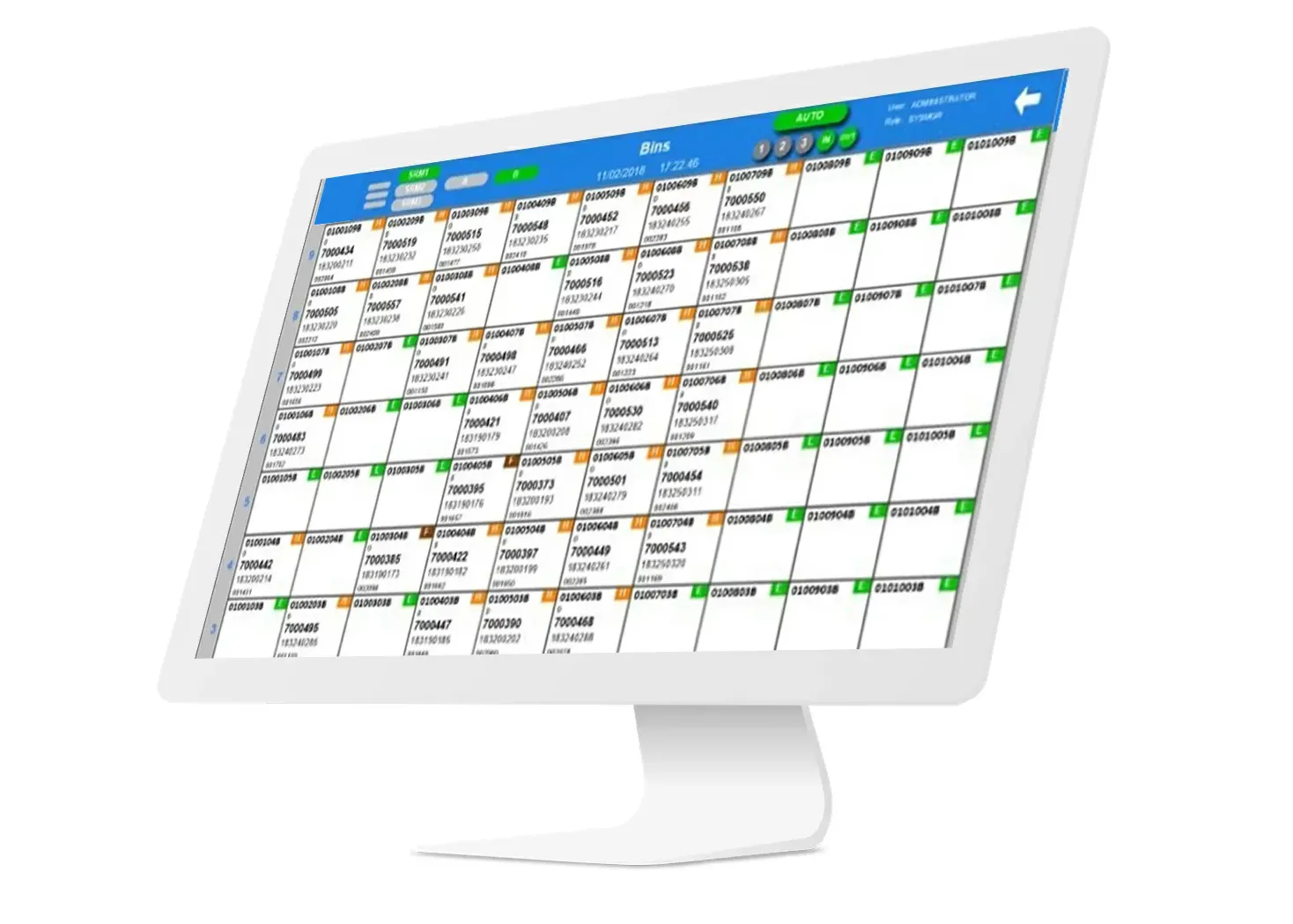
This screenshot shows storage contents and status, providing a visual view of what vehicles are stored in which bin along with their current status.
In the automotive industry, vehicle bodies are stored in the mixed bank after they have been painted and prior to making their way into the final assembly process. The mixed bank helps manufacturers set the sequence of vehicles moving into final assembly based on rules. For example, there may be a rule to limit the number of vehicles with a sunroof in order to maintain TAKT time. By using an AS/RS, material can be optimized for production.
Automating Decision Making
GE Vernova's Proficy software interfaces with AS/RS hardware in order to control the decision making of the overall system.
At a recent implementation for a major automotive OEM, our AS/RS application uses CIMPLICITY HMI/SCADA to monitor and visualize real-time status and Tracker, which delivers routing and control to manage the inbound and outbound routing. Inbound bodies are stored to optimize outbound crane utilization. Outbound bodies are selected based on a set of configurable business rules.
GE Vernova's AS/RS application provides the automotive OEM with:
At a recent implementation for a major automotive OEM, our AS/RS application uses CIMPLICITY HMI/SCADA to monitor and visualize real-time status and Tracker, which delivers routing and control to manage the inbound and outbound routing. Inbound bodies are stored to optimize outbound crane utilization. Outbound bodies are selected based on a set of configurable business rules.
GE Vernova's AS/RS application provides the automotive OEM with:
- Supervisory routing and control of the AS/RS hardware including conveyors and cranes. The software maintains a digital image of the storage inventory which is used to direct crane and conveyor operation.
- Visualization of the real-time status – Users can see where items are within the Mixed Bank as well as the status of each item at a glance.
- Hold Management – With hundreds of vehicles in storage, this capability places holds on individual items or groups of items, ensuring they do not get selected for movement on the general assembly line or Final Assembly.
- Alarm / Fault annunciation and reporting – Easily showing users where and when there are issues with the system, so they can address immediately.
- ASRS Historical Reporting
- High Availability for greater uptime and consistent operations.
Best Practices
GE Vernova's Professional Services
For some additional information on this customer’s application, I spoke to Don Walker who is a Senior Project Manager with our Professional Services team. Like myself, Don has spent a lot of time in automotive facilities over the years. He has managed many projects within our automotive customers and was heavily involved in the most recent AS/RS rollout we did.
Question: What value did the AS/RS system give to the customer?
Don Walker: The advantage that this new system has over the customer’s old system is that operators can see exactly where items are out on the floor. This information combined with alarm and status messages allow them to troubleshoot issues quickly and easily. And all screens are available on mobile devices, so users can access the system from anywhere.
With the logic built into the system, most of the time it is running on its own. Sometimes though things can go wrong in which case the Manual Control gives them the ability to fix issues.
For some additional information on this customer’s application, I spoke to Don Walker who is a Senior Project Manager with our Professional Services team. Like myself, Don has spent a lot of time in automotive facilities over the years. He has managed many projects within our automotive customers and was heavily involved in the most recent AS/RS rollout we did.
Question: What value did the AS/RS system give to the customer?
Don Walker: The advantage that this new system has over the customer’s old system is that operators can see exactly where items are out on the floor. This information combined with alarm and status messages allow them to troubleshoot issues quickly and easily. And all screens are available on mobile devices, so users can access the system from anywhere.
With the logic built into the system, most of the time it is running on its own. Sometimes though things can go wrong in which case the Manual Control gives them the ability to fix issues.
"The advantage that this new system has over the customer’s old system is that operators can see exactly where items are out on the floor. This information combined with alarm and status messages allow them to troubleshoot issues quickly and easily."
Don Walker - Senior Project Manager, GE Vernova's Proficy Professional Services
Question: We’ve been working with automotive customers for a long time. What benefit does that experience give to customers?
Don Walker: Leveraging what we’ve done with other automotive customers, we were able to put this system together quickly, providing significant implementation cost savings.
Question: Anything else you’d like to add?
Don Walker: The customer loves the support they get from our team.
Don Walker: Leveraging what we’ve done with other automotive customers, we were able to put this system together quickly, providing significant implementation cost savings.
Question: Anything else you’d like to add?
Don Walker: The customer loves the support they get from our team.
Ready for AS/RS?
If you’re a manufacturer, AS/RS can help you improve capacity in your facility with a more compact footprint, decrease errors in selecting materials, increase throughput with greater efficiency, and provide higher availability with a manufacturing buffer.
GE Vernova has both the proven Proficy software and expert Professional Services to deliver fast time to value with an AS/RS solution. Find out today how our team can improve your manufacturing efficiency.
GE Vernova has both the proven Proficy software and expert Professional Services to deliver fast time to value with an AS/RS solution. Find out today how our team can improve your manufacturing efficiency.