Customer Story Bar
TRAINING
TRACEABILITY
Customer Information
Introduction
Company
Eaton
Industry
Manufacturing & Digital Plant, Aerospace & Defense
Products
CIMPLICITY Extensions, Cloud MES, iFIX, Proficy Historian for Cloud, Proficy Plant Applications, Proficy Workflow, Tracking & Routing, MES - Manufacturing Execution Systems, Proficy Industrial Software
Reprinted with permission from Control Design magazine.
Improving Document Management in Complex Discrete Manufacturing
"We started our Proficy journey on the aerospace side of our business with 50 pages of documents for each of our 30,000 components," noted Mark Tudor, vice president, information technology, Eaton. Eaton was trying to solve several problems in turning to GE Vernova's Proficy software platform, number one being document management.
Improving Document Management in Complex Discrete Manufacturing
"We started our Proficy journey on the aerospace side of our business with 50 pages of documents for each of our 30,000 components," noted Mark Tudor, vice president, information technology, Eaton. Eaton was trying to solve several problems in turning to GE Vernova's Proficy software platform, number one being document management.
- Document management was being done in their ERP system where engineering information was stored in text fields, Tudor related.
- The design and quality information was scattered, and data was collected manually.
- Quality management couldn't perform global revisions if a common part changed, making change management difficult.
- The need for the operator to access several plant systems complicated training as well.
"Before this software upgrade, if we built something wrong, it was difficult to know; training costs were huge, as were the problems," said Tudor.
"Compliance relied on paper-based traceability methods and analytics were not seeing root causes. We had to store data manually, and there was a huge amount we needed to keep for as long as the plane was flying, 30 years or more."
Mark Tudor
Vice President, Information Technology, Eaton
In the past, complex discrete manufacturing required a large amount of information that was managed manually or in multiple systems that were tied together by the operator and production process.
Today, there are methods to enable a "digital thread" throughout these complex manufacturing operations.
A persistent digital thread
Better production decisions are enabled when data flows between systems and this digital thread stretches from engineering, through operations to shipping.
At Eaton, GE Vernova Proficy software is now connecting data to people, machines and processes. It is being used to pull everything together in this and other large, discrete manufacturing applications.
Today, there are methods to enable a "digital thread" throughout these complex manufacturing operations.
A persistent digital thread
Better production decisions are enabled when data flows between systems and this digital thread stretches from engineering, through operations to shipping.
At Eaton, GE Vernova Proficy software is now connecting data to people, machines and processes. It is being used to pull everything together in this and other large, discrete manufacturing applications.
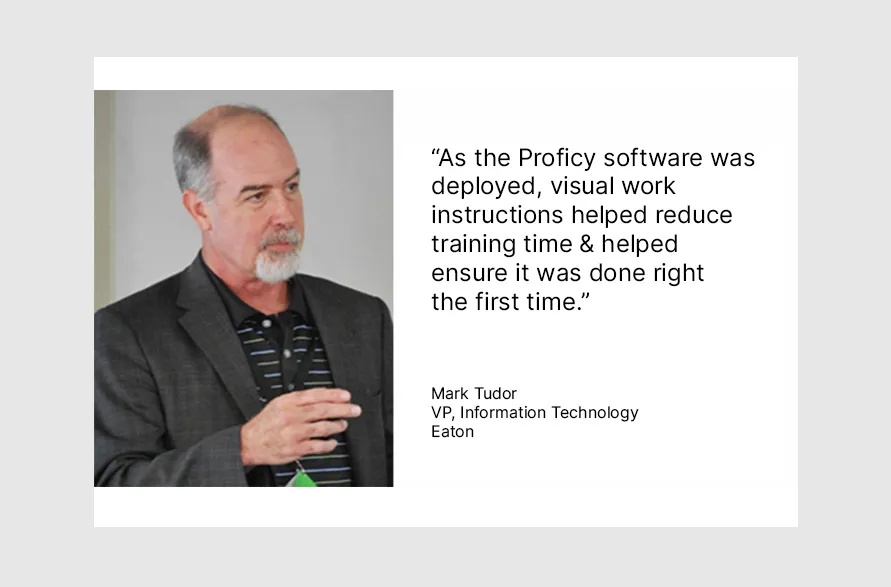
Image credit: GE Vernova
"The paperwork issues went away. We also leveraged standard work instructions and best practices across all sites. At the start we had 458 standard processes and reduced it to 87 with the new system in place."
Better control of and access to the documentation made record retention a built-in function, and global changes could be readily made.
Focus on Early Wins
Tudor noted some important lessons learned. One was to not underestimate how long it will take to pull design and production data out of ERP and into Proficy. He recommended a modular approach instead of doing it all at once.
“Break it down into small pieces and do it in phases," Tudor said. "Good definition of these phases is also important to 'box in' the work and to know when you are done."
"Focus on early, quick wins," he added. "We didn't have enough quick wins because we bit off more than we could chew at the start. However, once we cleaned up the data, manufacturing and engineering loved it. And the operators, once they learned the new system, were strong supporters."
Tudor also recommended that when starting out and scoping out what you are going to do, involve all parties including quality, operators, manufacturing, engineering, IT and the front office.
"Get all the folks involved so they understand the impact and benefits," he said.
Better control of and access to the documentation made record retention a built-in function, and global changes could be readily made.
Focus on Early Wins
Tudor noted some important lessons learned. One was to not underestimate how long it will take to pull design and production data out of ERP and into Proficy. He recommended a modular approach instead of doing it all at once.
“Break it down into small pieces and do it in phases," Tudor said. "Good definition of these phases is also important to 'box in' the work and to know when you are done."
"Focus on early, quick wins," he added. "We didn't have enough quick wins because we bit off more than we could chew at the start. However, once we cleaned up the data, manufacturing and engineering loved it. And the operators, once they learned the new system, were strong supporters."
Tudor also recommended that when starting out and scoping out what you are going to do, involve all parties including quality, operators, manufacturing, engineering, IT and the front office.
"Get all the folks involved so they understand the impact and benefits," he said.