Customer Story Bar
Introduction
A major European utility was facing challenges in inspecting/monitoring its critical electrical equipment, ensuring its employees’ safety during hazardous inspections, and keeping O&M costs low. Read below how they transitioned to lower cost, safer, and more efficient inspections using GE Vernova’s Autonomous Inspection.
Client
- A vertically integrated major European utility with a presence in conventional as well as renewables markets.
Challenges
- Monitoring critical electrical equipment while keeping costs low.
- Enabling remote asset inspections/monitoring by minimizing or eliminating the need to travel to the site for inspections.
- Ensuring employee safety during hazardous inspections.
Action
- Autonomous Inspection, along with fixed thermal cameras, was implemented at the customer site for automated and remote monitoring of electrical equipment. This involved Generator step-up transformers (GSUT) and Gas insulated switchyard inlets.
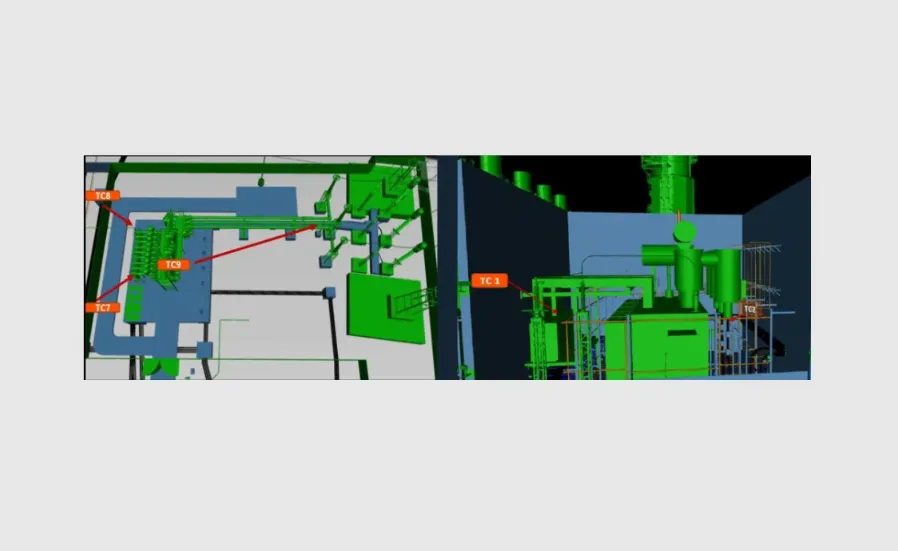
Thermal cameras and Autonomous Inspection application were set up at site to monitor electrical equipment such as Gas insulated Switchyard and Generator step-up transformers (GSUT)
Results
Autonomous Inspection enabled the customer to:
- Save on asset inspection costs and resources through remote monitoring of equipment.
Witness cost savings and productivity gains vs. available alternatives as sensors and instrumentation options were relatively expensive and disruptive - Achieve faster abnormality detection and response (vs. manual inspections) to prevent equipment downtimes.
- Monitor equipment surface temperature profile, receive alerts, and transfer temperature data to APM for advanced analysis.
- Maximize workers’ safety by eliminating need for them to be around equipment.
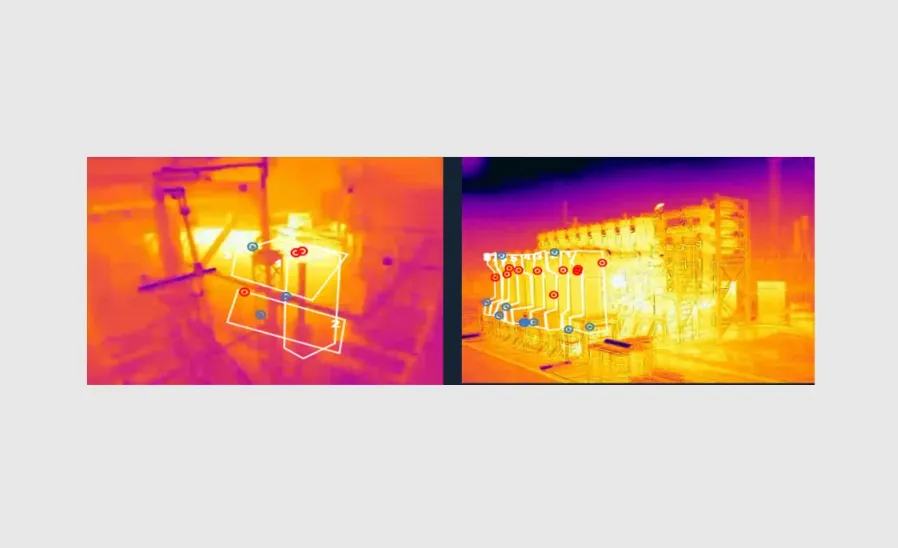
Output - Thermal images of Generator step-up transformers (GSUT) and Gas Insulated Switchyard
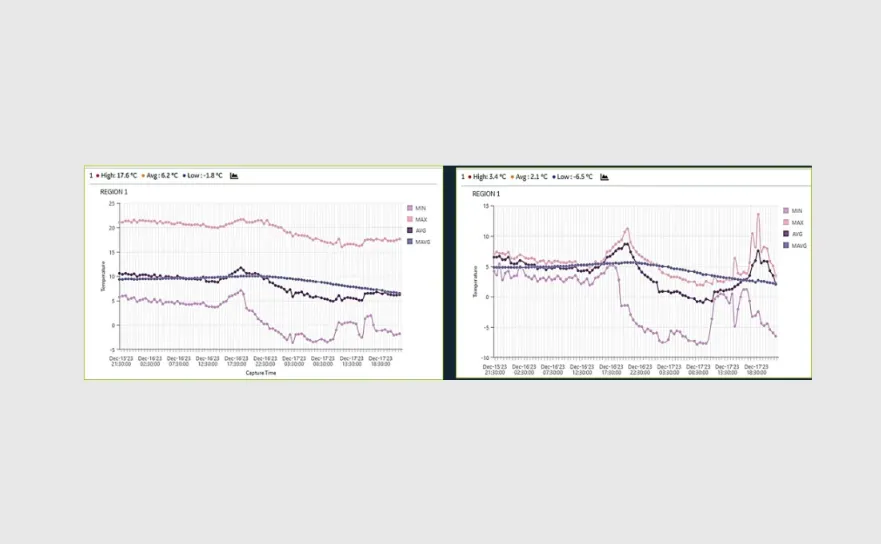
Output - Timeseries temperature graphs of regions monitored for Generator step-up transformers (GSUT) and Gas Insulated Switchyard