Electrify & Decarbonize with Software
GE Vernova’s Electrification Software business is enabling the energy transition through a suite of software products and services to help customers electrify and decarbonize the energy ecosystem.
Learn how our software is using artificial intelligence (AI) to develop real-time insights, and analyzing a variety of outcomes to orchestrate the complexity of managing different energy generation sources on the path to net zero.
Power of Artificial Intelligence
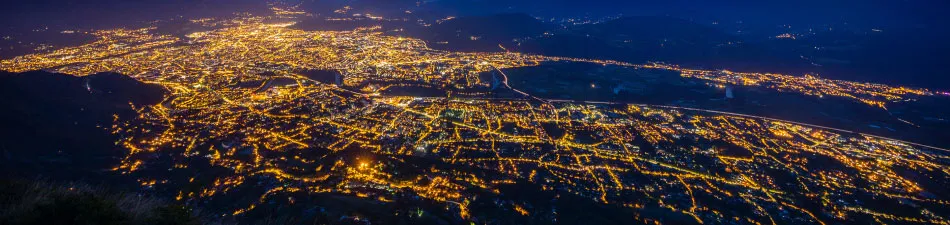

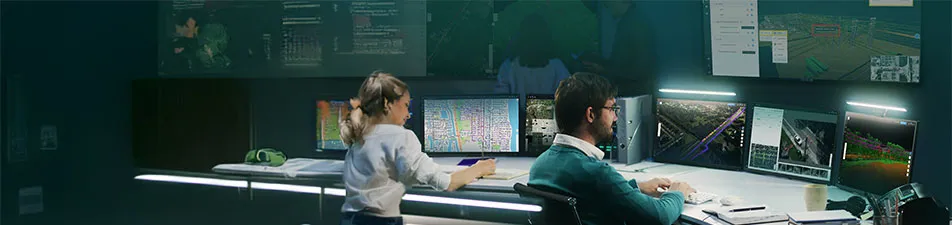
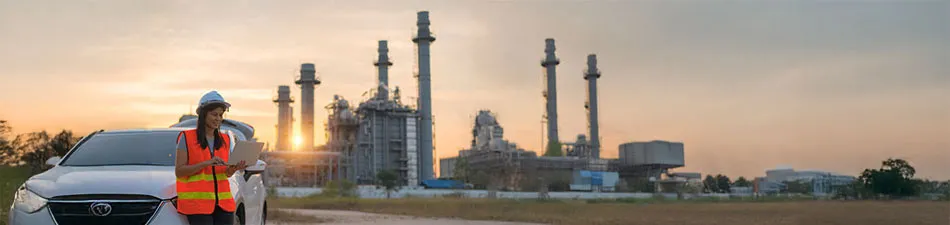
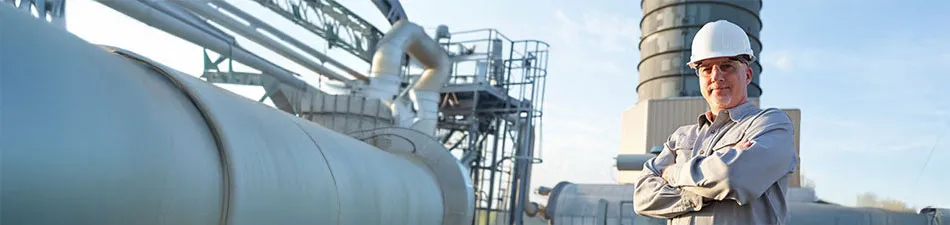
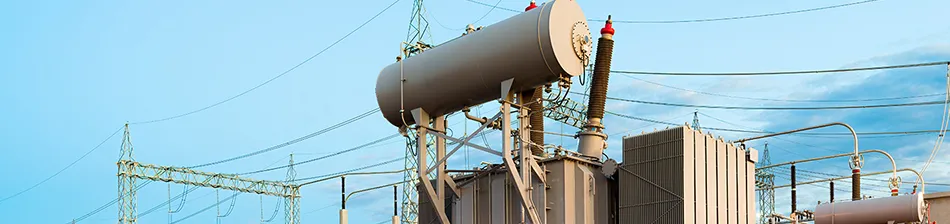
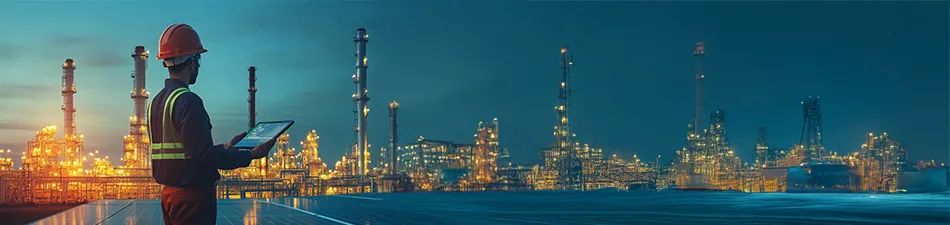
Energy Transition by Numbers
The energy transition cannot happen without digitization of data through software, which can solve the complexity, manage interconnected systems, leverage data at exponential scale, and make optimal real-time decisions under uncertainty.
75%
of Fortune 500 utilities use our grid software
90%
of companies across the sectors use our industrial software
33%
emissions accuracy engineered by our asset performance software
"The opportunities and challenges we confront as part of the energy transition are central to the future of our planet. Software plays a key role in solving them with urgency."
CEO, Electrification Software
Harness the Power of Data
The complexity of the energy transition requires software to play a pivotal role as the world drives towards electrification while simultaneously trying to decarbonize.
