Enterprise Integration: Enhancing Connectivity and Performance in Manufacturing Operations
Author Sticky
Understanding Enterprise Scale and the Role of Integration
Enterprise Scale refers to the ability of manufacturing operations to modernize quickly, improve performance across large sites and multiple plants, and reduce costs by leveraging scalable, flexible, standardized, and integrated systems. One of the critical capabilities of Enterprise Scale is Integration – the connection of systems across the enterprise to eliminate silos, improve efficiency, and enable real-time decision-making.
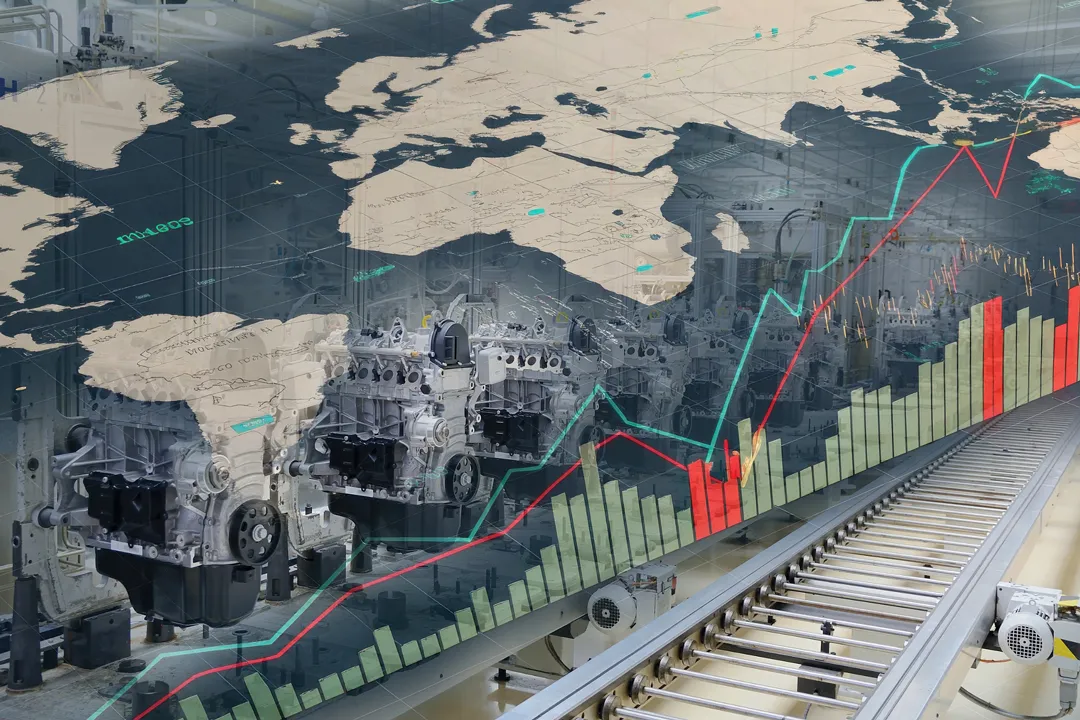
Image credit: GE Vernova
Why Enterprise Integration Matters for Operations, Engineering, and IT Leaders
For manufacturing enterprises, enterprise integration is not just about connecting systems; it’s about creating a unified operational framework that enables data-driven decision-making at every level. Without enterprise integration, critical insights remain trapped in silos, slowing response times and making it difficult to drive efficiencies at scale. Here’s why enterprise integration is essential for key stakeholders:
Operations Leaders need real-time visibility into production, maintenance, and scheduling to optimize efficiency and minimize downtime. Integrated systems allow them to track production progress across multiple sites, identify inefficiencies, and respond proactively to potential disruptions. By ensuring streamlined data flow between SCADA, MES, and scheduling platforms, operations leaders can maintain stable and predictable production environments.
Engineering Leaders require streamlined data aggregation and contextualization to support predictive maintenance, process improvements, and compliance. Without integration, engineers struggle with fragmented data that hinders root cause analysis and continuous improvement initiatives. A unified system enables them to connect historical performance trends with real-time production data, allowing for better predictive maintenance strategies and improved product quality.
IT Leaders must ensure secure, enterprise-wide data integration that supports scalability and AI-driven analytics while maintaining compliance. As organizations expand, IT teams face the challenge of managing increasing data complexity while ensuring security and compliance with industry regulations. Integrated solutions streamline data governance, improve cybersecurity protocols, and enable AI-driven insights that enhance operational decision-making.
By fostering streamlined integration, manufacturing enterprises can break down operational silos, improve collaboration between departments, and drive meaningful efficiency gains. A well-integrated ecosystem not only enhances visibility and security but also lays the foundation for innovation, enabling organizations to adapt to evolving industry demands with confidence.
Key Enterprise Integration Challenges and How to Overcome Them
Integration at an enterprise scale presents unique challenges that can hinder operational efficiency, data accessibility, and overall business performance. Many manufacturing organizations struggle with fragmented data sources and outdated infrastructure, making it difficult to achieve seamless connectivity across operations.
Without a strong enterprise integration strategy, businesses face inefficiencies that slow down decision-making, reduce agility, and increase security risks. Below, we explore the core challenges manufacturing organizations encounter when striving for enterprise-wide integration and the benefits of addressing them.
Without a strong enterprise integration strategy, businesses face inefficiencies that slow down decision-making, reduce agility, and increase security risks. Below, we explore the core challenges manufacturing organizations encounter when striving for enterprise-wide integration and the benefits of addressing them.
Challenge #1: Siloed Systems Preventing Unified Operations
Many manufacturing enterprises struggle with fragmented SCADA, MES, and Historian systems that operate independently, making it difficult to have a single view of operations and maintenance.
Operations Leaders: Managing multiple, disconnected systems slows down response times and creates inefficiencies in production oversight.
Engineering Leaders: Lack of unified data prevents efficient process optimization and predictive maintenance.
IT Leaders: Ensuring security and compliance across disparate systems is complex and time-consuming.
A unified operational view enables faster decision-making, smoother collaboration, and greater efficiency across the enterprise. Instead of battling disconnected systems and fragmented data, teams can focus on driving innovation, optimizing performance, and responding proactively to challenges. With integrated systems providing real-time insights, organizations can eliminate costly inefficiencies and create a more agile, resilient operation poised for long-term success.
Challenge #2: Disconnected Data Sources Preventing Enterprise-Wide Insights
Without centralized data aggregation, manufacturing enterprises struggle to generate timely and meaningful insights from operational data.
Operations Leaders: Limited access to cross-plant data reduces the ability to optimize production and respond proactively to issues.
Engineering Leaders: Inconsistent data formats across systems make it difficult to apply analytics and AI-driven improvements.
IT Leaders: Lack of integration complicates data governance and security protocols.
Making faster and more informed decisions leads to greater collaboration and ensures that teams work together seamlessly. By eliminating data silos and integrating systems, businesses can enhance efficiency, optimize performance, and build a data infrastructure that scales with the future of manufacturing operations. With this level of integration, companies can stay competitive, adapt to evolving industry needs, and drive meaningful innovation.
Challenge #3: Inefficient Traceability and Genealogy
Poorly contextualized data makes it difficult to track materials, personnel, and production steps accurately.
Operations Leaders: Compliance risks and quality issues arise due to gaps in traceability.
Engineering Leaders: Inefficient genealogy tracking prevents root cause analysis and process optimization.
IT Leaders: Securing data and driving consistency across traceability records is a challenge.
Ensuring compliance with manufacturing industry regulations, improving quality control measures, and gaining full transparency into operational processes are essential for maintaining efficiency and reliability. By integrating systems and centralizing data, businesses can track production with greater accuracy, minimize costly errors, and uphold the highest operational standards.
Challenge #4: Inability to Generate Timely, Actionable Insights
Legacy infrastructure and fragmented systems delay insight generation, reducing responsiveness to operational changes.
Operations Leaders: Lack of real-time data inhibits production optimization and prevents proactive adjustments to scheduling and resource allocation.
Engineering Leaders: Delayed insights make it harder to correct inefficiencies and address maintenance needs before they cause downtime or quality issues.
IT Leaders: Outdated systems limit AI and advanced analytics capabilities, preventing organizations from leveraging predictive maintenance and up-to-date insights.
Faster response times enable manufacturing organizations to react swiftly to operational challenges, minimizing disruptions and keeping production on track. Reduced downtime leads to greater efficiency and cost savings, while improved forecasting allows for better planning and resource allocation. By integrating critical systems, businesses can create a more resilient and adaptable operation that is ready to meet evolving industry demands.
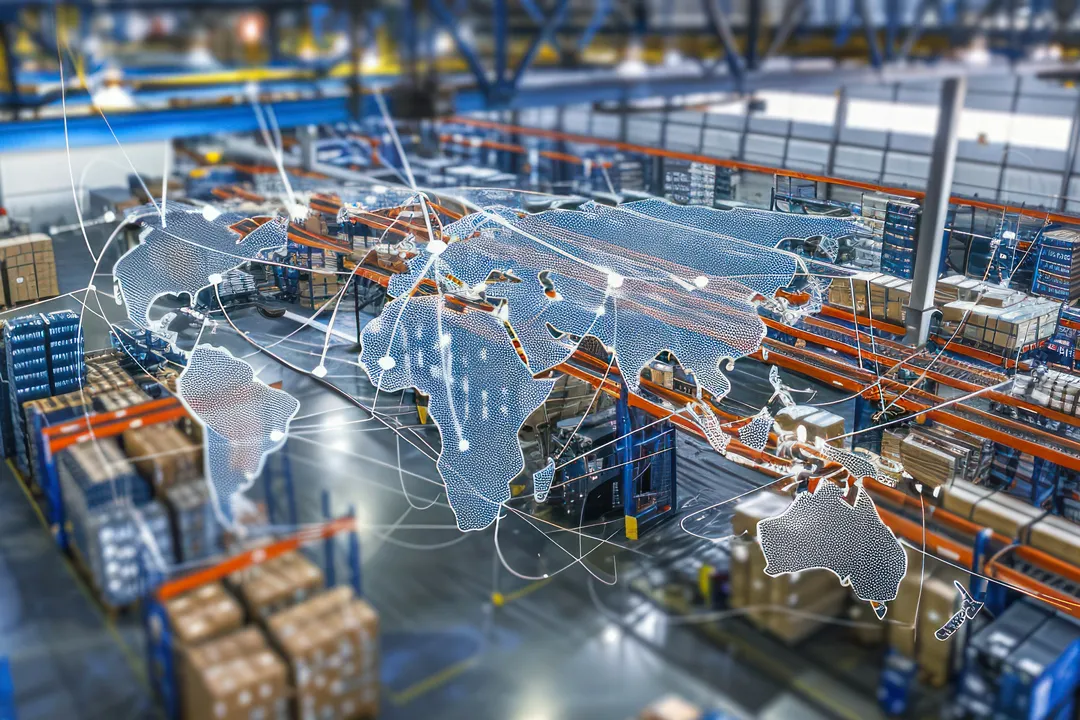
Image credit: GE Vernova
Challenge #5: Difficulty Achieving Comprehensive Oversight
Lack of a centralized view makes it difficult to monitor production from raw material intake to finished product shipment.
Lack of a centralized view makes it difficult to monitor production from raw material intake to finished product shipment.
Operations Leaders: Without a complete production view, identifying bottlenecks and inefficiencies is difficult.
Engineering Leaders: Limited visibility prevents proactive maintenance and process enhancements.
IT Leaders: Ensuring secure and streamlined integration across multiple production sites is a challenge.
Achieving end-to-end visibility allows manufacturing organizations to monitor and manage every stage of production with greater precision and control. Optimized production workflows reduce bottlenecks and inefficiencies, leading to smoother operations and increased output. With improved enterprise-wide coordination, teams can work more cohesively, ensuring that data and processes align seamlessly across departments and facilities.
Customer Case Study: JP Air Tech Improves Production Visibility with Proficy Scheduler
JP Air Tech, a manufacturer of air filters for various industries, needed a better way to manage production scheduling. Previously, the company relied on manual processes that resulted in lost orders, inefficient scheduling, and a lack of production visibility. By implementing Proficy Scheduler, JP Air Tech achieved a structured approach to scheduling that improved efficiency and reduced operational disruptions.
The Challenges:
- Lack of production visibility: Orders were frequently misplaced or forgotten, causing delays and inefficiencies.
- Manual scheduling inefficiencies: The company relied on Excel-based scheduling, which required constant updates and was prone to errors.
- Disjointed workflow: Operators had no clear system to follow, leading to miscommunications and disruptions in production.
The Outcomes:
- Increased production overview: A unified scheduling system provided full visibility into production workflows.
- More predictable production flow: Proficy Scheduler provided a structured, digital scheduling system that kept production on track and minimized internal mix-ups.
- Improved efficiency: Automated updates minimized redundant tasks, reducing manual intervention and scheduling errors.
- Enhanced adaptability: The company could easily adjust production in response to unplanned changes, improving responsiveness to operational challenges.
By implementing Proficy Scheduler, JP Air Tech experienced a 30-40% growth in production efficiency. The integration of scheduling with operations enabled a steady and predictable workflow, ensuring that no orders were lost or delayed. This transformation underscores the power of enterprise-wide integration in driving efficiency, visibility, and scalability in manufacturing operations.
Read the full case study on how JP Air Tech generates 30% growth Proficy Scheduler here.
Read the full case study on how JP Air Tech generates 30% growth Proficy Scheduler here.
How Proficy Enables Streamlined Enterprise Integration
Proficy Industrial Software and Services support Enterprise Scale by providing a comprehensive integration framework that connects critical manufacturing systems. Engineered to streamline data flow and provide interoperability across SCADA, MES, Historian, and Scheduling solutions, Proficy helps manufacturers to achieve enterprise-wide visibility, efficiency, and control. Below is a closer look at how each Proficy solution supports enterprise integration.
Proficy Manufacturing Execution System (MES)
Proficy Manufacturing Execution System (MES) brings together disparate production data into a single system, helping manufacturers achieve greater efficiency and fast-response operational insights.
- Centralized data management: Consolidates efficiency, traceability, performance, and genealogy data in one platform.
- Standardized processes: Reduces redundant data entry by providing a single contextual view of operational data.
- Enhanced traceability: Tracks materials, personnel, and production processes, ensuring compliance and quality control.
Proficy Operations Hub
Proficy Operations Hub is an operations intelligence software that acts as a digital command center, integrating information from various systems to provide a single source of truth for enterprise-wide decision-making.
- Quick operational insights: Combines data from SCADA, MES, and Historian for a comprehensive production overview.
- Improved decision-making: Supports faster response times by offering a visual representation of plant operations.
- Role-based access control: Manages access levels so stakeholders can securely view and interact with operational data based on their roles.
Proficy Historian
Proficy historian software supports up-to-date data access and advanced analytics by integrating multiple data sources into a single, AI-ready platform.
- Enterprise-wide data aggregation: Collects and normalizes data from SCADA, MES, and other operational systems.
- AI and analytics readiness: Provides structured, contextualized data for machine learning, predictive maintenance, and performance optimization.
- Secure and scalable architecture: Supports hybrid-cloud deployments, supporting data accessibility without compromising security.
Proficy Scheduler / ROB-EX
Proficy Scheduler / ROB-EX bridges the gap between scheduling, maintenance, inventory, and production planning, ensuring smooth operational flow.
- Optimized production scheduling: Aligns production schedules with maintenance, inventory levels, and supply chain demands.
- Adaptive rescheduling: Provides visibility into live production constraints, allowing for quick adjustments in response to disruptions.
- Streamlined ERP and MES integration: Synchronizes scheduling data with broader enterprise resource planning efforts, driving consistency across systems.
Bringing It All Together
By integrating these solutions, Proficy Software helps manufacturers to connect critical systems, reduce inefficiencies, and make data-driven decisions quickly. The ability to centralize operations, streamline scheduling, and enhance visibility across production processes allows manufacturing enterprises to scale effectively while maintaining agility. Whether optimizing manufacturing execution, improving data accessibility, or driving smooth scheduling operations, Proficy provides the integration backbone needed to achieve enterprise-wide efficiency and long-term success.
The Future of Enterprise Integration
Enterprise Integration is a critical capability for achieving Enterprise Scale and unlocking operational efficiency, scalability, and intelligent decision-making. By reducing data silos, providing fast-response insights, and enabling end-to-end traceability, Proficy Software helps manufacturing enterprises to modernize faster, improve performance, and reduce costs.
If you missed any of the previous blogs in our Enterprise Scale series, we encourage you to go back and explore how scalability , flexibility , and standardization contribute to a more efficient operation. Contact us today to learn more about how we can help your manufacturing organization achieve streamlined integration.
If you missed any of the previous blogs in our Enterprise Scale series, we encourage you to go back and explore how scalability , flexibility , and standardization contribute to a more efficient operation. Contact us today to learn more about how we can help your manufacturing organization achieve streamlined integration.
Contact Us