How Steel Manufacturers Can Enhance Quality Control and Optimize Processes
Author Sticky
Steel is the most commonly used and recycled metal in the world with over 3,500 recognized grades. It is literally everywhere in; cars, appliances, buildings, pipes, etc. Steel manufacturers are constantly challenged to develop steel with superior characteristics that meet a customer’s exacting specifications. To maintain market share, with mounting competition to produce more material faster, it is essential that steel manufacturers do not lose sight of quality.
Consistent Quality KPI
It’s not always about improving quality—think “consistency”
For many industrial organizations, one key performance indicator (KPI) is often “improve quality.” But, in steel manufacturing, it’s not necessarily about arbitrarily improving quality, it’s about delivering consistency. For specialty steel manufacturers in particular, who manufacture materials for construction projects or transformers, the end product must meet specific standards or regulations across the entire order.
The construction steel holding up the tallest buildings in the world has different characteristics than the steel used in jet engines. So, for steel producers, it’s not about improving the quality of those materials, it’s about making sure each order is fulfilled with steel that meets quality standards—every time, whether we are creating new peaks in a city skyline or helping improve aircraft efficiency. If it doesn’t, the result can be costly, both to the manufacturer and their end customer.
Many steel manufacturers produce on demand. So, there are precise quality and chemical specifications for each order. It’s crucial that this chemistry make-up is tracked from beginning to end—again to make sure quality standards are precise. If at any point in the manufacturing process a variation occurs the entire batch must be re-manufactured or sold as a less profitable grade.
For many industrial organizations, one key performance indicator (KPI) is often “improve quality.” But, in steel manufacturing, it’s not necessarily about arbitrarily improving quality, it’s about delivering consistency. For specialty steel manufacturers in particular, who manufacture materials for construction projects or transformers, the end product must meet specific standards or regulations across the entire order.
The construction steel holding up the tallest buildings in the world has different characteristics than the steel used in jet engines. So, for steel producers, it’s not about improving the quality of those materials, it’s about making sure each order is fulfilled with steel that meets quality standards—every time, whether we are creating new peaks in a city skyline or helping improve aircraft efficiency. If it doesn’t, the result can be costly, both to the manufacturer and their end customer.
Many steel manufacturers produce on demand. So, there are precise quality and chemical specifications for each order. It’s crucial that this chemistry make-up is tracked from beginning to end—again to make sure quality standards are precise. If at any point in the manufacturing process a variation occurs the entire batch must be re-manufactured or sold as a less profitable grade.
Challenges
How to address the challenge of traceability
So, how do you avoid this variability in the production process? Traceability is challenging for sure, but it can be done effectively. As you can imagine there is a lot to track in the manufacturing of steel materials. From the raw or recycled materials that come into a facility, to the melting at temperatures as hot as 1700°C (that’s hotter than volcanic lava) in blast furnaces, to miles upon miles of rollers, casting equipment, and ultimately fabrication, there are a myriad of variables to track and manage throughout manufacturing process. Being able to track the exact chemistry and specifications of each production run, the state of the equipment processing the materials, and the end-customer’s order request, is a requirement to drive business performance and remain competitive in today’s market.
So, how do you avoid this variability in the production process? Traceability is challenging for sure, but it can be done effectively. As you can imagine there is a lot to track in the manufacturing of steel materials. From the raw or recycled materials that come into a facility, to the melting at temperatures as hot as 1700°C (that’s hotter than volcanic lava) in blast furnaces, to miles upon miles of rollers, casting equipment, and ultimately fabrication, there are a myriad of variables to track and manage throughout manufacturing process. Being able to track the exact chemistry and specifications of each production run, the state of the equipment processing the materials, and the end-customer’s order request, is a requirement to drive business performance and remain competitive in today’s market.
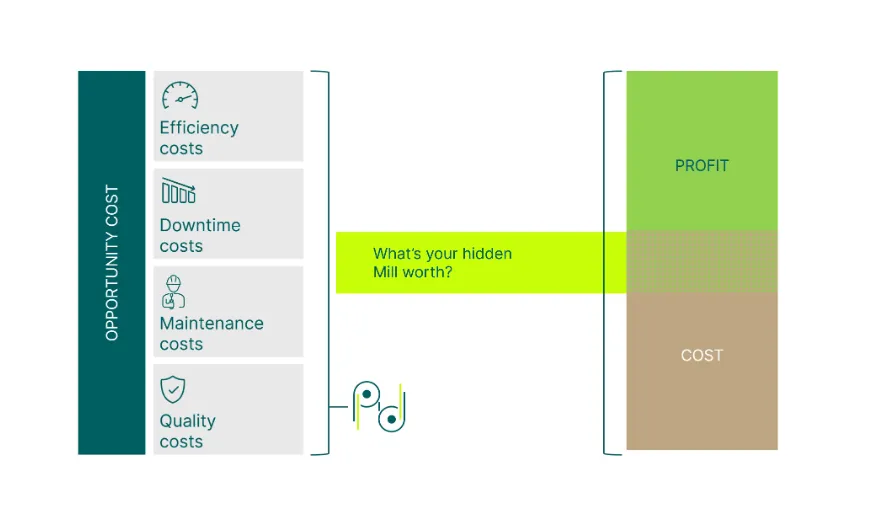
Industrial Applications
Implementing digital transformation to improve steel manufacturing
With an aging workforce and aging equipment, the status quo will continue to be a challenge for organizations looking to gain market share and improve their bottom line. By implementing industrial applications, such as asset performance management (APM) and manufacturing execution systems (MES) software, data can become the differentiator in your business process.
APM can help make sure your mill systems are delivering differentiated performance, avoiding unplanned downtime and optimizing your maintenance spend by shifting from reactive to proactive maintenance culture.
MES can help improve on-time delivery performance, optimize your operational costs, and ensure order specifications are met with consistency.
These two industrial applications enable your organization to make informed decisions, in near real-time, on the mill floor to optimize the manufacturing process and yield. And for executives, these industrial apps help provide improved visibility into production and performance data.
Using data as the differentiator enables steel producers to deliver the exact product requested, on time, and with consistent quality; which is now an expectation of world class suppliers.
Learn more about how GE Vernova is improving industrial operations in metals.
With an aging workforce and aging equipment, the status quo will continue to be a challenge for organizations looking to gain market share and improve their bottom line. By implementing industrial applications, such as asset performance management (APM) and manufacturing execution systems (MES) software, data can become the differentiator in your business process.
APM can help make sure your mill systems are delivering differentiated performance, avoiding unplanned downtime and optimizing your maintenance spend by shifting from reactive to proactive maintenance culture.
MES can help improve on-time delivery performance, optimize your operational costs, and ensure order specifications are met with consistency.
These two industrial applications enable your organization to make informed decisions, in near real-time, on the mill floor to optimize the manufacturing process and yield. And for executives, these industrial apps help provide improved visibility into production and performance data.
Using data as the differentiator enables steel producers to deliver the exact product requested, on time, and with consistent quality; which is now an expectation of world class suppliers.
Learn more about how GE Vernova is improving industrial operations in metals.